Выбор посадок подшипников качения на валы и в корпуса
Надежность работы подшипниковых узлов в значительной степени зависит от правильного выбора посадок колец подшипников на вал и в корпус.
При выборе посадки учитываются: тип подшипника; частота вращения; нагрузка на подшипник (постоянная или переменная по значению и направлению, спокойная или ударная); жесткость вала и корпуса; характер температурных деформаций системы (увеличение или уменьшение натягов при рабочих температурах); способ крепления подшипника (с затяжкой или без затяжки); удобство монтажа и демонтажа.
Различают три основных вида нагружения колец: кольцо вращается относительно радиальной нагрузки, подвергаясь так называемому циркуляционному нагружению; кольцо неподвижно относительно радиальной нагрузки и подвергается местному нагружению; кольцо нагружено равнодействующей радиальной нагрузкой, которая не совершает полного оборота, а колеблется на определенном участке кольца, подвергая его колебательному нагружению.
На рис. 5.27 приведены основные виды нагружения колец подшипников, а в табл. 5.12 - характеристика нагружений .
Рис. 5.27.
Посадку выбирают гак, чтобы вращающееся кольцо подшипника было смонтировано с натягом, исключающим возможность его проскальзывания по посадочной поверхности в процессе работы под нагрузкой; другое кольцо при этом должно монтироваться с зазором. В этой связи:
1) при вращающемся вале необходимо иметь неподвижное соединение внутреннего кольца с валом; наружное кольцо соединять с корпусом с небольшим зазором;
2) при неподвижном вале внутреннее кольцо должно иметь посадку на валу с необходимым зазором, а наружное кольцо - неподвижную в корпусе.
В подшипниках качения различают исходный, монтажный и рабочий зазор. Исходный зазор подшипник имеет в свободном состоянии. Согласно ГОСТ 24810-81 по типам подшипников установлены условные обозначения групп зазоров (обозначают арабскими цифрами)
а одну из них словом "нормальная"). Группы различаются размерами радиального и осевого зазоров. Монтажный зазор получается в подшипнике после его сборки в изделии. Вследствие посадки одного кольца с гарантированным натягом монтажный зазор всегда меньше исходного. Наиболее важным в подшипнике является рабочий зазор - зазор между телами качения и дорожками качения при установившемся рабочем режиме и температуре. При значительном рабочем зазоре возникает большое радиальное биение, а нагрузка воспринимается меньшим числом шариков; при рабочем зазоре, близком к нулю, нагрузка распределяется на наибольшее число шариков, поэтому подшипник в данном случае обладает большей долговечностью.
Монтаж подшипника с натягом производят преимущественно по тому кольцу, которое испытывает циркуляционное нагружение.
При циркуляционном нагружений колец подшипников посадки выбирают по интенсивности радиальной нагрузки Рн на посадочную поверхность. Допускаемые значения Рн, подсчитанные по средним значениям посадочных натягов, приведены в табл. 5.14.
Интенсивность нагрузки подсчитывают по формуле
где Рг - радиальная нагрузка на опору; АГ" К2, Кг - коэффициенты; Ь - рабочая ширина посадочного места (А = В - 2г, где В - ширина подшипника; г - координата монтажной фаски внутреннего или наружного кольца подшипника).
Динамический коэффициент посадки К{ зависит от характера нагрузки: при перегрузке до 150 %, умеренных толчках и вибрации К{ = 1; при перегрузке до 300 %, сильных ударах и вибрации АГ, = 1,8. Коэффициент К2 (табл. 5.15) учитывает степень ослабления посадочного натяга при полом вале или тонкостенном корпусе; при сплошном вале К2 = 1. Коэффициент Кг учитывает неравномерность распределения радиальной нагрузки Fr между рядами роликов в двухрядных конических роликоподшипниках или между сдвоенными шарикоподшипниками при наличии осевой нагрузки Ftl на опору.
Значения Кг (табл. 5.16) зависят от величины (Т;,//7,)^/^/?- угол контакта тел качения с дорожкой качения наружного кольца, зависящий от конструкции подшипника). Для радиальных и радиально-упорных подшипников с одним наружным или внутренним кольцом Кг = I.
С увеличением радиальной нагрузки возрастает ее интенсивность />я(5.71), а следовательно, повышается натяг в посадках.
В посадках подшипников классов 0 и 6 применяют поля допусков 7-го квалитета для отверстий корпусов и 6-го квалитета - для валов. Посадки подшипников классов 5 и 4 осуществляют точнее, чем классов 0 и 6, на один квалитет.
Выбрать посадку циркуляционно-нагруженного внутреннего кольца радиального однорядного подшипника 0-308 (класс точности 0; ё ~ 40 мм; О - 23 - 2-2,5 - 18 мм) на вращающийся полый вал <іх ~ 20 мм. Радиальная реакция опоры Ря - 4119 Н. Нагрузка ударная, перегрузка 300%, осевой нагрузки на опору нет.
Решение. 1. Находим коэффициенты: А", = 1,8; = 1,6 (так как --- = 0,5; - = 2,25); К5 = 1 (так как Р0 = 0).
2. Находим интенсивность нагрузки по формуле (5.71):
В табл. 5.14 заданным условиям для вала соответствует поле допуска кв (так как класс точности подшипника 0), образующее с полем допуска кольца посадку с натягом (А/га|п = 2 мкм, А/га4, ~~ 30 мкм). Отклонение диаметра ё подшипника принимаем по ГОСТ 520-89 (верхнее 0, нижнее - 12 мкм), а отклонение вала - по ГОСТ 25347-82 соответственно (ез- +18 мкм, е ~ +2 мкм).
Посадку можно определить также по минимальному натягу между циркуляционно-нагруженным кольцом и поверхностью сопрягаемой с ним детали. Приближенно минимальный натяг
где радиальная нагрузка; N - коэффициент (для подшипников легкой серии равен 2,8, средней - 2,3 и тяжелой - 2).
По найденному значению Л^п выбирают ближайшую посадку.
Наибольший натяг посадки не должен превышать допускаемого (Л^ < Л^оп) во избежание разрыва колец подшипника:
где [ст] - допускаемое напряжение при растяжении (для подшипниковой стали [ст] = 400 МПа).
Основные размеры подшипников качения устанавливает ГОСТ 3478-2012 , который распространяется на шариковые и роликовые радиальные, радиально-упорные, упорно-радиальные и упорные подшипники качения, устанавливает предпочтительные присоединительные размеры подшипников и наибольшие предельные радиусы галтелей вала и корпуса.
Допуски и предельные отклонения размеров подшипников качения по ГОСТ 25256-82 .
ГОСТ 520-2011 устанавливает для разных типов подшипников качения классы точности: - нормальный, 6, 5, 4, Т, 2
- для шариковых и роликовых радиальных и шариковых радиально-упорных подшипников; - 0, нормальный, 6Х, 6, 5, 4, 2
- для роликовых конических подшипников; - нормальный, 6, 5, 4, 2
- для упорных и упорно-радиальных подшипников. Классы указаны в порядке повышения точности.
Класс точности указывается перед условным обозначением подшипника через разделительную черту, например, 6-308, 5-36210
; в случае отсутствия дополнительных требований, класс точности 0
не указывается, например 7306
.
Поля допусков и технические требования к посадочным поверхностям валов и корпусов устанавливает ГОСТ 3325-85 .
Посадки подшипников качения осуществляют: в корпус – в системе вала, на вал – в системе отверстия. Это означает, что предельные отклонения присоединительных размеров D и d не зависят от посадок. Поле допуска размера D наружного кольца является основным валом и обозначается буквой l (латинская "эль" ) с указанием класса точности подшипника, например:l0, l6, l5 , предельные отклонения D зависят от типа и класса точности подшипника (табл.13) .
Поле допуска размера d
внутреннего кольца является основным отверстием и обозначается прописной буквой L
и классом точности, например L0, L6, L5, L4
. В отличие от основного отверстия H
по ГОСТ 25346-82, поля допусков внутренних колец подшипников расположены в «тело», т.е. в минус, ES = 0
.
Допуски размеров колец не совпадают с допусками IT
и при ведены в табл.13
в соответствии ГОСТ 520-2011.
Посадки образуются применением полей допусков (ГОСТ 25346-82) для корпуса и вала и полей допусков наружного и внутреннего колец подшипника (ГОСТ 520-2011) и показаны на рис. 1
.
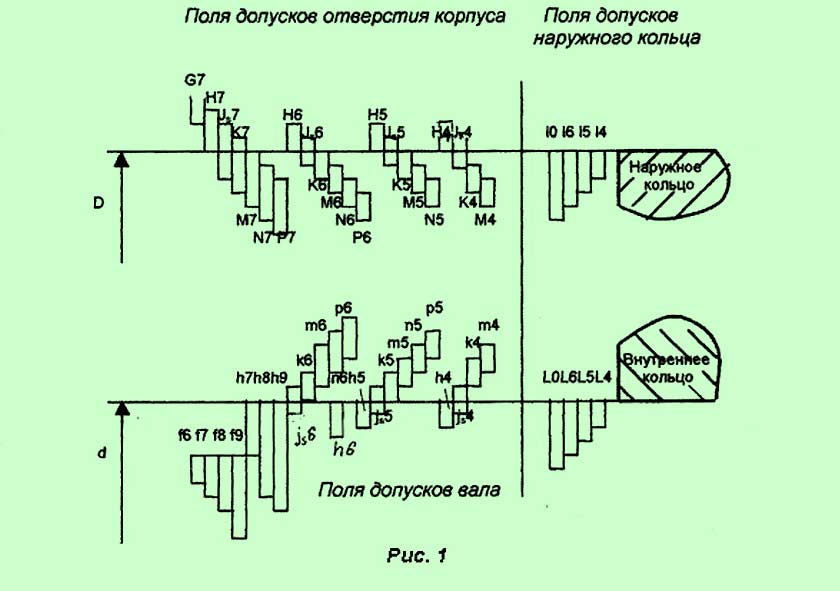
К посадочным поверхностям под подшипники качения предъявляют повышенные требования к точности формы и качеству поверхности. Отклонения формы поверхностей корпусов и валов не должны превышать для подшипников 0
и 6
классов значений, равных IT/4
, а для подшипников 5
и 4
классов – IT/8
.
Наиболее значительное отрицательное влияние на работоспособность подшипников качения оказывают конусообразность и овальность посадочных поверхностей, поэтому для этих поверхностей указывают допуск круглости и допуск профиля продольного сечения.
Шероховатость поверхностей устанавливается в зависимости от класса точности подшипника и диаметра (табл. 12)
.
Выбор посадок подшипников качения
Посадки подшипников качения на вал и в корпус зависят от вида нагружения, величины и характера нагрузок, размера и конструкции подшипника, класса точности подшипника.
Различают три вида нагружения подшипников (ГОСТ 3325-85): местное,циркуляционное и колебательное
.
При местном нагружении
нагрузка воспринимается ограниченым участком дорожки кольца.
При циркуляционном нагружении
радиальная сила воспринимается последовательно всеми элементами дорожки качения.
Колебательное нагружение
– комбинированный вид нагружения.
В случае местного нагружения основное отклонение принимается по табл.7
в зависимости от размера, конструкции корпуса (разъемный, неразъемный), уровня перегрузок.
При циркуляционном нагружении посадка выбирается на основе расчета совместных деформаций колец, возникающих вследствие натяга при посадке вращающегося кольца на вал или корпус, с учётом условия обеспечения оптимального радиального зазора в зоне сопряжения тел качения с поверхностью дорожки качения. В упрощенном виде этот расчет сводится к вычислению интенсивности нагружения P R :
P R = (Fr×k 1 ×k 2 ×k 3)/B
где: Fr- расчетная радиальная сила, действующая на опору;
B - посадочная ширина подшипника, мм;
k 1 - коэффициент, учитывающий динамические перегрузки;
k 2 - коэффициент, учитывающий ослабление посадки при полом вале или тонкостенном корпусе;
k 3 - коэффициент, учитывающий влияние осевых сил на перераспределение радиальных сил по рядам тел качения, в случае применения двухрядных конических роликовых подшипников или сдвоенных шарикоподшипников.
Значения k 3 зависят от величины
Fa×ctgα/Fr
где Fa – осевая сила; α - угол контакта, град.
Значения коэффициентов k 1 , k 2 , k 3
находят из табл. 9, 10 и 11
.
В случае циркуляционного нагружения основное отклонение, сопряженной с подшипником детали, принимают по табл.8
, исходя из рассчитанного P R
, с учетом диаметра и класса точности подшипника.
Допуски корпусов или валов при местном нагружении кольца подшипника принимают по 7
-му квалитету точности (IT7)
, если подшипник 0
-го или 6
-го класса и по IT6
, если 5
-го или 4
-го класса.
Допуски корпусов или валов при циркуляционном нагружении кольца принимают по 6
-му квалитету (IT6)
при классе точности подшипника 0
или 6
и по IT5
для 5
-го или 4
-го класса.
Примеры расчета посадок подшипников качения
Рассмотрим пример расчета и выбора посадок подшипников качения, входящих в представленный на рис. 2 узел.
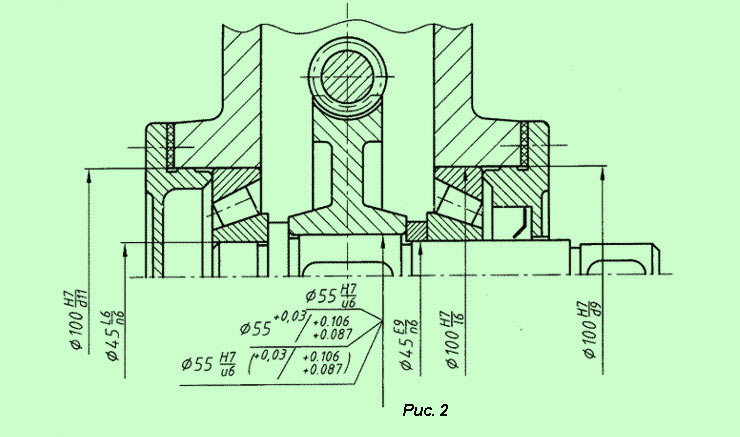
Исходные данные:
подшипник 6-7309
– однорядный конический, 6
-го класса точности;
радиальная реакция опоры Fr = 20000 Н
;
условия работы – удары, вибрация, перегрузка до 300%
;
вал – полый с диаметром отверстия d 1 = 20 мм
;
корпус неразъемный; вращается вал, корпус – неподвижен.
1. По справочнику находим посадочные размеры подшипника – диаметр наружного кольца – D = 100 мм , внутреннего – d = 45 мм , посадочная ширина, т.е. ширина без учёта радиусов закругления – B = 26 мм ;
2. Нижние предельные отклонения колец определяем по табл.13
– eiD = -0,013 мм
, EId = -0,01 мм
, верхние отклонения равны 0
, тогда D = 100 -0,013 , d = 45 -0,01
.
Вид нагружения колец: наружное – местное, внутреннее – циркуляционное.
3. Основное отклонение корпуса находим по табл.7
с учетом того, что: корпус неразъемный, перегрузка 300%
, D = 100 мм
., получим основное отклонение – Н
.
Поле допуска отверстия корпуса с учетом класса точности подшипника – Н7
.
Посадка наружного кольца в корпус – 100Н7/l6
. Пользуясь табл. 1 и табл. 2
строим схему расположения полей допусков (рис. 3а
).
4. Основное отклонение валов определятся по интенсивности нагружения P R
. Для этого необходимы коэффициенты, входящие в уравнение.
Коэффициент k1 = 1,8
(табл.9)
, с учетом перегрузки 300%
;
k2 = 1,6
, т.к. d1/d = 20/45 = 0,44
, а отношение наружнего и внутреннего диаметров подшипника D/d = 100/45 = 2,22
;
k3 = 1,0
, поскольку подшипник однорядный.
Вычислим интенсивность нагружения:
P R = (20000/26)×1,8×1,6×1,0 =2215 Н/мм .
Допуски и посадки подшипников качения
Для сокращения номенклатуры подшипники изготавливают с отклонениями размеров наружного и внутреннего диаметров не зависимо от посадки, по которой их будут монтировать. Для всех классов точности подшипников верхнее отклонение присоединительных диаметров принято равным нулю. Таким образом, диаметры наружного и внутреннего колец приняты соответственно за диаметры основного вала и основного отверстия, а следовательно, посадку соединения наружного кольца подшипника с корпусом назначают в системе вала, а посадку соединения внутреннего кольца подшипника с валом – в системе отверстия. Однако поле допуска на диаметр отверстия внутреннего кольца расположено в «минус» от номинального размера, а не в «плюс», как у обычного основного отверстия, т.е. не в «тело» кольца, а вниз от нулевой линии (рис. 49).
Такое расположение поля допуска установлено с целью обеспечения сравнительно небольшого натяга в соединении внутреннего кольца подшипника с валом при использовании имеющихся в ЕСКД полей допусков на валы под переходные посадки, с учетом, что в большинстве подшипниковых соединений вращается вал, а корпус с наружным кольцом неподвижны.
Посадка подшипника в корпус в этих же условиях, как будет показано в дальнейшем, должна быть с небольшим зазором, поэтому поле допуска на диаметр наружного кольца располагается в «тело» детали или в «минус», как принято в общем машиностроении для основного вала.
Вследствие овальности конусообразности и других отклонений формы при измерении могут быть получены различные значения диаметра колец подшипников в разных сечениях. В связи с этим стандартом установлены предельные отклонения номинальных , и средних , диаметров колец. Средние диаметры и определяют расчетом как среднее арифметическое наибольшего и наименьшего диаметров, измеренных в двух крайних сечениях кольца.
К шероховатости посадочных и торцовых поверхностей колец подшипников, а также валов и корпусов предъявляют повышенные требования. Например, у колец подшипников класса точности 4 и 2 диаметром до 250 мм параметр шероховатости должен быть в пределах 0,63…0,32 мкм. Особое значение имеет шероховатость поверхности дорожек и тел качения. Уменьшение параметра шероховатости поверхности от 32…0,16 мкм до 0,16…0,08 мкм повышает ресурс подшипника более чем в два раза, а дальнейшее уменьшение параметра шероховатости до 0,08…0,04 мкм – еще на 40 %.
Выбор посадок колец подшипников на вал и в корпус осуществляется согласно ГОСТ 3325-85, исходя из условий работы сборочной единицы, в которую входят подшипники. При этом учитываются: схема работы сборочной единицы (вращается вал с внутренним кольцом или корпус с наружным кольцом); вид нагружения колец и режим работы подшипника.
Практически чаще всего сборочные единицы, содержащие подшипники, работают по схеме, когда вращается внутренне кольцо с валом, а наружное кольцо и корпус неподвижны (рис. 50). В этом случае необходимо обеспечить неподвижность соединения внутреннего кольца подшипника с валом. Это достигается за счет использования полей допусков валов под переходные посадки (основные отклонения , , , ), что, благодаря специфическому расположению поля допуска внутреннего кольца (вниз от нулевой линии), позволяет получить в соединении небольшой, чаще всего гарантированный натяг. Исключение представляет случай, когда предельные отклонения вала расположены симметрично относительно нулевой линии. Однако в этом случае вероятность получения натяга в соединении достаточно велика (96…98 %).
Рис. 50. Схемы полей допусков посадок колец подшипников на вал и в корпус
при вращении вала с внутренним кольцом подшипника
Применять для рассматриваемого соединения валы с полями допусков под неподвижные посадки недопустимо, так как получаемые при этом натяги сильно осложняют условия монтажа и демонтажа подшипников, а в процессе их эксплуатации возможны поломки в связи со значительными внутренними напряжениями в кольцах и шариках и заклинивание тел качения.
Поля допусков валов, как видно из рис. 50, выбирают по системе основного отверстия:
Для подшипников класса точности 0 и 6 − , , , ;
Для подшипников класса точности 5 и 4 − , , , ;
Для подшипников класса точности 2 − , , , .
Если вращается наружное кольцо с корпусом, а внутреннее кольцо и вал неподвижны, то в этом случае необходимо обеспечить неподвижность соединения наружного кольца с корпусом. Соединение внутреннего кольца с валом в рассматриваемом случае должно быть свободным. Поля допусков для отверстий корпусов и поля допусков на валы приведены в справочной литературе по нормированию точности подшипников.
Выбор посадок колец подшипников определяется также видом нагружения и режимом работы.
В случае если сборочная единица работает по схеме, вращается вал с внутренним кольцом, а корпус с наружным кольцом неподвижны, возможны две типовые схемы нагружения подшипника.
Первая типовая схема (рис. 51, а ). Радиальная нагрузка постоянна по величине и направлению. В этом случае внутреннее кольцо подшипника испытывает циркуляционное нагружение , а наружное кольцо – местное нагружение.
При местном нагружении (рис. 51, б ) кольцо подшипника воспринимает радиальную нагрузку , постоянную по направлению, лишь ограниченным участком беговой дорожки и передает ее ограниченному участку корпуса. Поэтому сопряжение наружного кольца подшипника с корпусом должно быть осуществлено по посадке с небольшим средневероятным зазором. За счет наличия зазора данное кольцо в процессе работы под действием отдельных толчков, сотрясений и других факторов будет периодически проворачиваться в корпусе, вследствие чего износ беговой дорожки станет более равномерным и долговечность подшипника существенно возрастет.
Циркуляционное нагружение создается на кольце при постоянно направленной радиальной нагрузке, когда место нагружения последовательно перемещается по окружности кольца со скоростью его вращения (рис. 51, в ). Посадка вращающегося циркуляционно нагруженного кольца должна обеспечивать гарантированный натяг, который исключает возможность относительного смещения или проскальзывания кольца и вала. Наличие вышеуказанных процессов приведет к развальцовке сопрягаемых поверхностей, потере точности, перегреву и быстрому выходу сборочной единицы из строя.
а б в
Рис. 51. Первая типовая схема нагружения подшипника и виды нагружения колей:
а – типовая схема нагружения; б – местное нагружение наружного кольца; в – циркуляционное нагружение внутреннего кольца
Рис. 52. Вторая типовая схема нагружения подшипника и виды нагружения колей:
а – типовая схема нагружения; б – колебательное нагружение наружного кольца
Вторая типовая схема (рис. 52, , схема которого, аналогичная схеме, представленной на рис. 52, в.
Режим работы подшипника принимается в зависимости от его расчетной долговечности. При расчетной долговечности более 10000 часов режим считается легким, при 5000…10000 часов − нормальным и при 2500…5000 часов − тяжелым. При ударных и вибрационных нагрузках, которые испытывают, например, трамвайные и железнодорожные буксы, валы дробильных машин и т.п., режим считается тяжелым независимо от расчетной долговечности.
Система допусков и посадок для подшипников качения
Подшипники качения - наиболее распространенные стандартные сборочные единицы, изготовляемые на специализированных заводах. Они обладают полной внешней взаимозаменяемостью по присоединительным поверхностям, определяемыми наружным диаметром D наружного кольца и внутренним диаметромd внутреннего кольца, и искомой внутренней взаимозаменяемостью между телами качения и кольцами.
Градация точности подшипников качения. Взаимозаменяемость подшипников качения определяется следующими требованиями к точности:
1) точностью присоединительных размеров d, D, ширины кольцаВ ; точностью формы и расположения поверхностей колец подшипников и их шероховатости;
2) точностью вращения, характеризуемой радиальным и осевым биениями дорожек качения и торцов колец;
3) точностью рабочего зазора g - зазора между телами качения и дорожками качения при установившемся рабочем режиме и температуре. Чем меньше зазор, тем равномернее распределяется нагрузка на тела качения.
С учетом требований к точности по ГОСТ 520 − 89 установлено пять классов точности подшипников, обозначаемых (в порядке повышения) 0; 6; 5; 4; 2. Для большинства механизмов общего назначения применяют подшипники класса точности 0. Подшипники более высоких классов точности применяют при больших частотах вращения и в случаях, когда требуется высокая точность вращения вала (например, для шпинделей шлифовальных и других прецизионных станков, для авиационных двигателей, приборов). Класс точности указывают через тире перед условным обозначением подшипника,
например 6− 205 (6− класс точности подшипника).
Подшипники качения – очень нежные детали, имеют тонкие, хрупкие кольца и в свободном состоянии подшипники имеют овальность. Но при монтаже на вал кольца принимают правильную цилиндрическую форму, и овальность исчезает.
Для обеспечения взаимозаменяемости подшипников качения овальность и средняя конусообразность отверстия и наружной цилиндрической поверхности колец не должны превышать 50% допуска на диаметры D m ,d m . Средние диаметрыd m иD m определяют расчетом как среднее арифметическое наибольшего и наименьшего диаметров, измеренных в двух крайних сечениях кольца:
D m = D max2 + D min; d m = d max2 + d min.
В связи с этим допуски для подшипников качения назначаются на следующие размеры:
1) на D иd ;
2) на D m иd m ;
3) на В .
Система допусков и посадок на подшипники качения основана на ЕСДП
Допуски и отклонения колец подшипников зависят только от класса точности подшипника и его габаритов и не зависят от характера соединения с валами и корпусами. Это делается для снижения номенклатуры подшипников качения. Характер соединения колец подшипника с валами и корпусами достигается только лишь за счет изменения поля допуска вала и поля допуска отверстия, то есть при посадке внутреннего кольца подшипника качения на вал применяется система отверстия, а при посадке наружного кольца – система вала.
Поля допусков обоих колец подшипника направлены в «− », то есть располагаются ниже нулевой линии (рис. 1).
Рис. 1. Схемы расположения полей допусков на диаметры колец подшипников качения отверстий в корпусах и валов (отклонения в мкм)
Благодаря перевернутой системе отверстия, применяемой для получения посадок внутреннего кольца на вал и используя отклонения j s ,k ,m ,n , получаем соединения и посадки с гарантированным натягом, которые в обычных гладких цилиндрических соединениях обеспечивают переходные посадки.
В системе отверстия применяются следующие поля допусков валов.
Поля допусков валов |
|
точности | |
f 6,g 6,h 6,j s 6 (j 6),k 6,m 6,n 6,p 6,r 6,h 7 |
|
g 4,h 4,j s 4,k 4,m 4,n 4,g 5,h 5,j s 5 (j 5),k 5,m 5,n 5 |
|
h 3,j s 3,g 4,h 4,j s 4,k 4,m 4,n 4 |
Для посадки наружного кольца в корпус, в системе вала предусмотрены следующие поля допусков отверстий.
Поля допусков отверстий |
|
точности | |
E 8,H 8,G 7,H 7,J s 7 (J 7),K 7,M 7,N 7,P 7 |
|
H 5,J s 5,K 5,M 5,G 6,H 6,J s 6 (J 6),K 6,M 6,N 6,P 6 |
|
H 4,J s 4,H 5,J s 5,K 5,M 5 |
Выбор посадок подшипников качения. Посадки следует выбирать так,
чтобы вращающееся кольцо подшипника было посажено с натягом, исключающим возможность обкатки и проскальзывания этого кольца по посадочной поверхности вала или отверстия в корпусе в процессе работы под нагрузкой; другое кольцо должно быть установлено с зазором.
Выбор посадок производится в зависимости от следующих факторов:
1) от класса точности;
2) от того, какое кольцо сажается – внешнее или внутреннее;
3) от величины и характера действующих нагрузок;
4) от вида нагружения.
Различают три вида нагружения:
1) местное;
2) циркуляционное;
3) колебательное.
1) При местном нагружении действует одна радиальная нагрузка, постоянная по величине и направлению в одной точке посадочной поверхности кольца подшипника и передается одной и той же точке посадочной поверхности вала или корпуса.
Местно нагруженные кольца необходимо устанавливать с зазором для постепенного проворачивания кольца во избежание местных выработок колец, валов и корпусов.
2) При циркуляционном нагружении действует одна радиальная нагрузка, которая передается последовательно всей окружности беговой дорожки подшипника и воспринимается также последовательно посадочной поверхностью вала или корпуса. Циркуляционно нагруженные кольца необходимо устанавливать на вал или корпус с натягом.
3) При колебательном нагружении действуют две радиальные нагрузки, из которых одна постоянна по величине и направлению, а вторая – вращающаяся. Равнодействующая этих двух нагрузок воспринимается ограниченным участком беговых дорожек колец подшипника и передается ограниченному участку посадочной поверхности вала или корпуса.
При колебательном нагружении оба кольца подшипника должны иметь переходный характер соединения с валами и корпусами с большей вероятностью получения зазора для проворачивания.
В зависимости от характера нагружения колец подшипника можно рекомендовать поля допусков для валов и отверстий (табл. 7.4)
Примеры условного обозначения требований к точности деталей подшипникового узла даны на рис. 2.
Рис. 2. Обозначение посадок подшипников качения на сборочных чертежах (а ) и полей допусков на чертежах деталей (б ):
1 − вал;2 − втулка;3 − корпус;4 − крышка;5 − колесо
Поскольку применение системы отверстия для соединения внутреннего кольца подшипника с валом и системы вала для соединения наружного кольца с корпусом является обязательным, на сборочных чертежах посадки колец подшипников принято обозначать одним полем допуска, например 40k6 ,90H7 в случае, если класс точности подшипника указан в технической документации.
Если класс точности подшипника не указан, то посадка обозначается следующим образом.
По внутреннему кольцу: 40 L k 6 6 , 40L 6 –k 6, 40L 6 /k 6.
По наружному кольцу: 90 H l 6 7 , 90H 7 –l 6, 90H 7 /l 6.
Поле допуска вала, отверстия, подшипника качения указывается в численном виде: 90H7 (+0,035 ).
Шероховатость посадочных поверхностей колец подшипников классов точности от 0 до 2-го достаточно малая. Так, шероховатость поверхностейRa валов и отверстий в корпусах должна находиться в пределах от 2,5 до 1,25 мкм для посадки подшипников нулевого класса и в пределах от 1,25 до 0,32 мкм и менее для посадки подшипников 6, 5 и 4-го классов.
Шарикоподшипники радиальные однорядные по своему конструктивному устройству способны воспринимать, наравне с радиальной нагрузкой, и небольшие осевые нагрузки, действующие в обе стороны вдоль оси вала.
Шарикоподшипники радиальные однорядные способны работать при больших числах оборотов, чем подшипники других конструктивных разновидностей, но соответствующих габаритов. Предельно допустимые числа оборотов радиальных однорядных шарикоподшипников могут быть повышены благодаря применению специальных режимов смазки, установке подшипников высокого класса точности, а также применением подшипников с сепараторами из антифрикционных материалов (текстолит, латунь, бронза, дюралюминий).
Шарикоподшипники радиальные однорядные имеют наименьшие потери на трение по сравнению с подшипниками других типов, имеющими соответствующие габариты.
Для хорошей работоспособности шарикоподшипников в механизмах необходим оптимальный радиальный зазор. Под начальным радиальным зазором подшипника качения подразумевается свободное пространство между телами качения и кольцами в диаметральном направлении, которое имеет подшипник в несмонтированном состоянии.
Начальный радиальный зазор после монтажа может существенно измениться под влиянием посадочных натягов, формы посадочных мест, изменения температуры колец подшипника и деталей подшипникового узла во время эксплуатации, нагрузки, отклонения от соосности посадочных мест и ряда других причин.
Начальные радиальные зазоры шарикоподшипников.
Основной ряд.
Внутренний диаметр подшипников:
d до 10мм - зазор от 0,005 до 0,016 мм.
d свыше 10 до 18мм - зазор от 0,008 до 0,022 мм.
d свыше 18 до 30мм - зазор от 0,010 до 0,024 мм.
Также выпускаются подшипники с уменьшенным и с увеличенным начальным радиальным зазором.
Классы точности подшипников.
Классы точности подшипников характеризуются значениями предельных отклонений размеров, формы, взаимного положения поверхностей подшипников.
Для шарикоподшипников установлены следующие классы в порядке повышения точности: 8, 7, нормальный, 6, 5, 4, Т, 2. по ГОСТ520-2002.
Допускаемые отклонения на посадочные размеры подшипников по ГОСТ520-2002.
Эскиз 203 подшипника с допусками на размеры и допусками формы и расположения поверхностей.
Посадки подшипников.
Посадки подшипников выбирают в зависимости от режима работы, вида нагружения и класса точности.
Режимы работы - тяжелый, нормальный, легкий.
Виды нагружения - циркуляционное, местное, колебательное.
Подшипники коленвала: Режим работы - тяжелый.
Виды нагружения:
Наружное кольцо подшипника - местное.
Внутреннее - циркуляционное.
Подготовка к монтажу посадочных мест.
Шероховатость и отклонения от геометрической формы посадочных поверхностей валов и отверстий корпусов, а также допуски выполняются в соответствии с требованиями ГОСТ 3325-85.
Эскиз посадочных мест под 203 подшипник нормальной точности в соответствии с ГОСТ 3325-85.
Посмотрим эскиз посадочных мест.
Допуск на изготовление отверстия = 0,016мм.
Допуск цилиндричности отверстия = 0,006мм.
Допуск на изготовление вала = 0,011мм.
Допуск цилиндричности вала = 0,003мм.
Риторический вопрос: Можно ли без последующей станочной обработкивосстановить изношенные посадочные места под подшипники методом накернивания, напайки, наваривания, подкладывания различной фольги и т.п.?
Детали механизмов, предназначенные для монтажа подшипников, с наличием на посадочных поверхностях забоин, коррозионных налётов, с отступлениями от правильной геометрической формы не должны допускаться к монтажу.
Годные посадочные места вала и корпуса перед монтажом смазать.
Обращение с подшипниками качения.
Не следует преждевременно вынимать подшипник из упаковки. Только непосредственно перед монтажом подшипник должен быть распакован и промыт в бензине или в горячем минеральном масле. Вращать сухие подшипники не следует. Чтобы предохранить подшипник от коррозии, не следует брать его не защищенными руками. Для этого следует пользоваться перчатками или чистой салфеткой. Перед монтажом подшипники смазать.
Монтаж подшипников.
Во всех случаях монтажа подшипников качения необходимо избегать передачи усилий при запрессовке через тела качения. Монтаж подшипника необходимо производить на вал через внутреннее кольцо и в корпус через наружное кольцо.
Неправильный и небрежный монтаж является одной из основных причин преждевременного выхода из строя во время эксплуатации.
Литература:
1. Шариковые и роликовые подшипники. Каталог - справочник. Москва 1963г.
2. ГОСТ520-2002.
3. ГОСТ 3325-85.